Knorr-Bremse and Continental have completed a milestone in the demonstration of automated driving
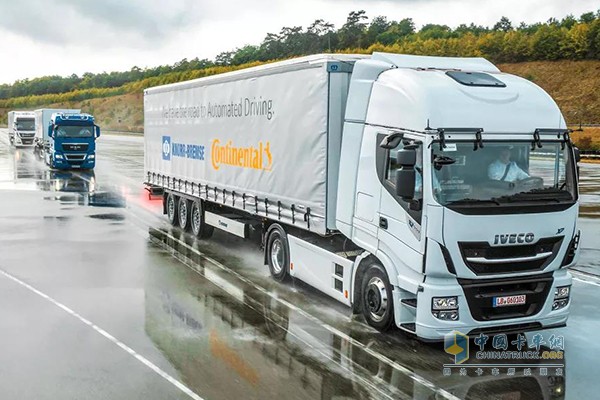
Highly automated driving is one step closer
This automatic line-up (ie, column) is a leader in the global brake system market, a leading supplier of other critical safety systems for rail vehicles and commercial vehicles, and a technology company from Hannover based on three different manufacturers. The combination of the trucks and the fleeted vehicle demonstrations was jointly developed. At the test site, initial test runs and demonstrations have been performed to the customer.
Through this lined demonstration, the partners demonstrated the autonomous driving features they could develop with the OEM. This includes team formation, following the car, emergency braking, cycling and disbanding. In the development process, special attention is paid to the control of the driver's control of the vehicle to the vehicle's self. The key factor to achieve this transfer is that there are very clear operational instructions, and the driver receives this information through a specially designed human-computer interaction interface. The interface displays information graphically and clearly, which allows the driver to clearly track system status at all times.
Camera, radar, lidar: data fusion processing for different sensors, providing a more accurate and reliable environmental field of view
As long as the partner vehicles in the queue are very close together, the transmission can be initiated by pressing the button. The emergency braking function of the synchronous vehicle-to-vehicle (V2V) ensures safer traffic: By initiating synchronous braking of all vehicles, the delay of no response time, the vehicle stops at the same distance as when driving.
Now, this provides customers with a test platform that can be lined up regardless of the brand of the vehicle and lays the foundation for further development of the technology. “Through the walk-through demonstration, we have reached the first milestone of our cooperation. The focus now is on sharing ideas with automakers to further develop system solutions based on the customer's product strategyâ€, Continental's commercial vehicle and aftermarket business Gilles Mabire, head of the department, said.
“Autonomous driving is a continuous evolutionary development. As a leading supplier of driver assistance products for commercial vehicles, our experience is an important foundation. The technology continues to improve and our understanding of the market continues to increase. This has changed the autonomous driving. The conditions and the speed at which the autopilot function is introduced, so the main focus of development changes. When it comes to customer needs and implementation paths, flexibility and openness are the key to our success, and we are passionate about maintaining close communication with our customers. This also means that we can showcase our product and functional roadmaps, create vehicle demonstrations and react quickly to meet our customers' and market needs.†Knorr-Bremse Executive Board member, responsible for commercial vehicle business Dr. Peter Laier added. Partners are also preparing to further develop the autopilot system on the highway, namely highway cruising.
Technical complement of system solutions
The technical solution for the line-up demonstration shows how the two technologies complement each other. Continental is responsible for the perception: the installation of sensors equipped with the latest technology, including cameras, radar and lidar sensors, plus V2V communication technology, to ensure that the vehicles travel safely with a very short distance between the lines, so that the very short distance of the line Make automatic driving more fuel efficient.
In order to handle sensor signals -- including those with other vehicles (V2V) or transportation infrastructure (V2X) - a development environment for demonstrations was built. To this end, the model of the corresponding environment is also created from the data to achieve self-control of the truck. In the future, the system will use Continental's central Auxiliary & Autopilot Control Unit (ADCU) and Knorr-Bremse's Global Extensible Brake Control (GSBC) to provide input into driving strategies.
The technical solution for the pilot demonstration shows how the technologies of Knorr-Bremse and Continental can complement each other.
In order to plan the trajectory of the vehicle, Knorr-Bremse has developed its expertise in the field of commercial vehicle dynamic systems. Most importantly, Knorr-Bremse is ensuring driving stability ("motion control") and execution-level requirements, transforming the driver's decision into a specific control process inside the vehicle, and initiating steering and braking to achieve vertical and horizontal vehicle visibility. control.
Knorr is also responsible for handling system integration including verification. As a result, commercial vehicle manufacturers can not only rely on Knorr-Bremse's experience, but they also have a well-defined partner to connect with the autopilot theme.
Highway cruise research and development work has begun
The experience gained by Continental and Knorr in the development of the pilot demonstration will further lay the foundation for a high degree of autopilot-highway cruising. Its technology enables bicycles to be driven automatically on the highway, and the first demonstration will be held next year. Starting in 2020, partners will be ready to develop this technology with manufacturers.
Reading volume: Source: Knorr-Bremse Commercial Vehicle Systems Author: No QThe domestic current situation of the die-casting mould
Die Casting Mould industry has developed rapidly in our country, the total output growth significantly, domestic die casting mold production after the United States, has become the second in the world, become the veritable die-casting superpower. It can have such achievement because of our country with unique broad market advantages and relatively cheap labor force. Depend on very obvious price in the international trade market, we produced the die casting mould which occupies a bigger superiority, according to the situation, in the future Chinese die casting industry development prospects are very broad.
The designing of die
casting tooling
1, According to the materials, shape and precision product, analyze technology,
decide of the process.
2, Confirm the location of product in the mold cavity. Analyze parting surface,
overflow system and the gating system.
3, Design the various activities of the core are assembled and fixed method.
4, Design the core-pulling distance and force.
5, Design the ejection device.
6, Confirm the die casting machine, design the mould base and the cooling
system.
7, Checking the mould size and die casting machine, drawing the process
flowchart and component of die casting mold.
8, Design is complete.
Die-casting mould making flowchart
Aluminum injection mould material and materials and its properties
Material of aluminum die casting mould: H13, ASSAB DIEVAR, SKD6;
Mould base: #45 steel, standard mould base (LKM);
Hardness after treatment: RHC 48~52;
Standard Configuration: Cooling system;
Tolerance: 0.1mm;
Machining equipment: CNC gantry milling machine, middle-speed WEDM machine, slow-feeding EDM, die spotting machine;
Mould life: 50000 shots ~ 100000 shots;
Lead time of die casting mould: 40 days-60 days.
What is the Moldflow analysis, this conception derived fromtaiwan. it's a precess through the computer for injection molding simulation by data simulate software, and get data result. Then assess the feasibilty of the mold program through these results to perfect mold and production designation.The common software for plastic mold such as moldflow, moldex 3D and so on. And the common software for Aluminum Die Casting Parts such as PROCAST, FLOW 3D and so on.
The conventional materials of die casting core, insert, slider
Production of die casting mould and QC control
Die Casting Mould
Aluminum Die Casting Mould, Zinc Die Casting Mould, Die Casting Mould, Die Cast Mold
NINGBO BEILUN LEMA MACHINERY TECHNOLOGY CO.,LTD , http://www.china-lema.com